Preventive maintenance software is more than just a digital solution—it’s a mindset rooted in routine, care, and foresight. That idea is at the heart of everything we do here at UpkeepRecord.com. Founded by Sam, a hands-on homeowner and mom of two, Upkeep Record was born from a lifelong love of fixing, organizing, and staying ahead of life’s maintenance curve. From scribbling notes in a logbook to creating streamlined seasonal checklists, this platform champions proactive maintenance for real life.
Sam’s inspiration started young—watching her parents keep things in order with just a calendar, a toolbox, and a lot of consistency. Today, she’s translated that same spirit into tools and guides that help people like you prevent breakdowns, save money, and stay sane. And in 2025, nothing embodies that mission better than the right preventive maintenance software.
Whether you’re managing home assets, fleet vehicles, industrial machines, or facilities, this guide will walk you through the core benefits, strategies, top platforms, and how to make implementation feel less like a headache and more like peace of mind.
Don’t miss our real-world breakdown of truck preventive maintenance for applied examples of how this software works in specific industries.
Table of Contents
Understanding Preventive Maintenance Software
What Is Preventive Maintenance Software and Why It Matters
Preventive maintenance software is a tool that helps you schedule, track, and manage maintenance tasks before problems arise. Instead of reacting to breakdowns, it empowers businesses and homeowners to plan ahead—automatically generating service alerts, work orders, and inspections based on time, usage, or condition.
This software is commonly used in manufacturing, property management, fleet services, and even home systems. With preventive maintenance software, you shift from a “fix-it-when-it-breaks” mindset to a proactive model that reduces repair costs and keeps everything running smoothly.
But why is this important now more than ever?
Because delays and failures are expensive. Equipment downtime leads to revenue loss, customer dissatisfaction, and safety risks. Using preventive maintenance tools helps ensure your operations flow without disruption—and with far fewer surprises.
Key Features That Define Effective Preventive Maintenance Solutions
The best preventive maintenance software platforms offer a core set of smart features:
- Automated Scheduling: Never forget a service again. The system sends reminders or auto-generates tasks based on your chosen rules.
- Work Order Management: Track task status, assign technicians, attach notes and photos—all in one place.
- Asset History Tracking: See the full maintenance history of equipment, including parts replaced and cost of repairs.
- Inventory and Parts Management: Avoid delays by knowing exactly which parts are in stock, where they’re located, and when to reorder.
- Mobile Access: Perform inspections, close tasks, and upload photos from any device on the go.
- Reporting & Analytics: See trends, detect recurring issues, and optimize maintenance schedules.
Discover great ideas like reliability-centered maintenance that can integrate with your software strategy to boost performance even further.
These capabilities don’t just make work easier—they save real time and money. In fact, companies that implement preventive maintenance software typically report 15%–25% fewer equipment failures and up to 30% longer asset lifespans.
Looking for inspiration? Try this page where we’ve explored how consistency in routines—even for home life—creates smoother outcomes.
How Preventive Maintenance Software Works
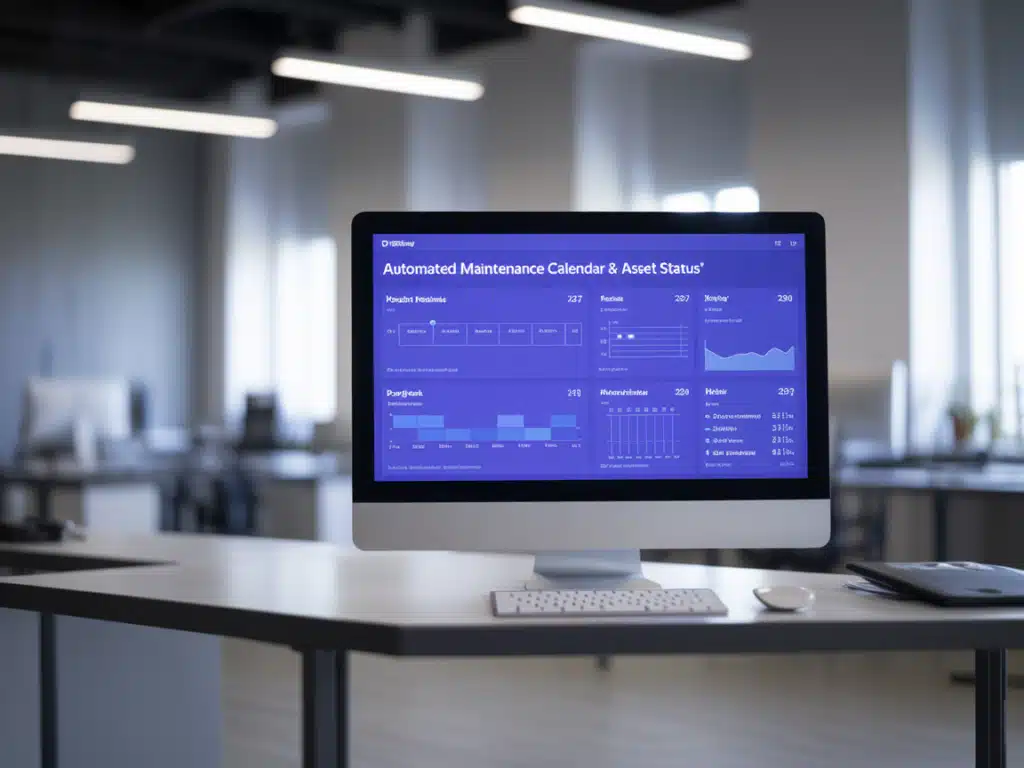
Overview of Functionality and Workflow Automation
At its core, preventive maintenance software acts like your behind-the-scenes maintenance manager—automating, assigning, and tracking every task that keeps your assets in top condition. But what does that actually look like in practice?
Here’s a simplified flow of how preventive maintenance software functions:
Step | Function | Example |
---|---|---|
1 | Asset Registration | You add machines, vehicles, or property systems into the software with details like serial numbers, location, and specs. |
2 | Schedule Setup | Based on usage hours, mileage, or calendar dates, you define when maintenance should occur. |
3 | Automated Task Generation | The software triggers work orders at the right time or usage threshold. |
4 | Technician Assignment | Assign internal staff or external vendors to complete tasks and close them digitally. |
5 | Mobile Updates & Feedback | Use a mobile app to upload photos, comments, and status updates in real-time. |
6 | Reporting & Analysis | View dashboards to analyze trends, downtime, and asset health. |
This kind of automation reduces the guesswork and paperwork involved in traditional maintenance. Instead of relying on manual logs or whiteboards, you have an organized digital command center.
Don’t miss our truck preventive maintenance guide for a detailed real-world example of how these systems perform in commercial fleets.
How It Integrates with CMMS and EAM Systems
If you’ve heard of CMMS (Computerized Maintenance Management Systems) or EAM (Enterprise Asset Management), you might wonder where preventive maintenance software fits in. Think of it like this:
- CMMS focuses on maintaining equipment and facilities.
- EAM takes a broader approach, covering the full lifecycle of assets—including acquisition, operation, maintenance, and disposal.
Preventive maintenance software often exists within a CMMS or EAM platform or as a standalone module that syncs with them.
Integration benefits include:
- Real-Time Asset Data Sync: Updates in asset condition, part usage, or status are shared across departments.
- Cross-Department Coordination: Facilities, procurement, and operations can all collaborate from a unified platform.
- Predictive Maintenance: When combined with IoT sensors, your software can initiate maintenance based on real-time performance.
For example, a sensor detects rising vibration in a motor. The software flags it, creates a task, notifies the technician, and logs the issue—automatically.
This level of insight and control would be impossible with spreadsheets alone, and it explains why platforms like Upkeep, Fiix, and MaintainX are gaining serious traction.
Check out this resource to learn more about our founder’s commitment to making complex systems feel accessible and easy to manage.
Benefits of Using Preventive Maintenance Software
Cost Savings and Downtime Reduction
One of the most compelling reasons to invest in preventive maintenance software is its proven ability to lower operational costs. By scheduling maintenance before a failure happens, businesses can avoid the high price of emergency repairs, lost productivity, and unplanned downtime.
Consider this: reactive maintenance often costs 3–9 times more than preventive action. Why? Because unplanned failures cause:
- Overtime labor costs
- Production delays
- Asset replacement expenses
- Extended downtime from diagnosis to resolution
With preventive maintenance software, you don’t just react—you plan, schedule, and act proactively. Here’s how that looks:
- Scheduled Maintenance keeps machinery in peak condition, reducing the risk of breakdown.
- Inventory Control ensures the right parts are always available, cutting repair delays.
- Mobile Access speeds up task completion, allowing techs to check in remotely.
Real-world businesses using digital maintenance platforms report up to 40% fewer unexpected outages and 30% lower repair costs annually.
Don’t miss our practical insights in this reliability-centered maintenance guide—it’s a complementary strategy that leverages software to extend asset life.
Improved Asset Reliability and Lifecycle Management
Every asset you own—from HVAC systems to vehicles to production lines—has a lifespan. The goal of preventive maintenance software is to maximize that lifespan through timely inspections, repairs, and tune-ups.
Here’s what it empowers you to do:
- Monitor Equipment Health: Track wear patterns, service intervals, and critical performance data.
- Extend Useful Life: Maintain optimal operating conditions, reducing strain and degradation.
- Document Service History: Prove compliance, spot recurring issues, and support smarter decision-making.
With centralized data, you also gain visibility into underperforming assets and make evidence-backed decisions like whether to repair, replace, or repurpose.
That’s a game changer for organizations looking to increase uptime and ROI. It’s also a core part of staying compliant with industry standards like ISO 55000 or OSHA.
Looking for inspiration? Try browsing our About page to see how smart upkeep practices translate into real-world simplicity, even for busy families and small operations.
Types of Preventive Maintenance Strategies in Software
Time-Based vs. Usage-Based Preventive Maintenance
Preventive maintenance software supports multiple maintenance models—and understanding the differences is key to building an efficient schedule.
Time-Based Preventive Maintenance
This is the most common and straightforward approach. Maintenance is scheduled at fixed intervals—monthly, quarterly, or annually—regardless of actual usage. It’s ideal for:
- HVAC systems
- Fire safety inspections
- Building-wide systems
Pros:
- Simple to implement
- Ensures consistent upkeep
Cons: - May result in unnecessary maintenance
- Doesn’t account for actual wear or usage
Usage-Based Preventive Maintenance
This model schedules tasks based on runtime, mileage, or other usage metrics. It’s particularly effective for:
- Fleet vehicles
- Manufacturing machinery
- Equipment with varying operational hours
Pros:
- More accurate than time-based methods
- Avoids over- or under-servicing
Cons: - Requires usage tracking integration
- Slightly more complex setup
With the right software, usage tracking is automated via sensors, counters, or technician input. Maintenance events are triggered when thresholds are hit, ensuring the task is timely and necessary.
Check out this truck preventive maintenance article for an excellent real-world example of usage-based maintenance in action.
Predictive and Condition-Based Maintenance Approaches
While traditional preventive strategies are proactive, newer models are intelligent—responding to real-time conditions and patterns.
Condition-Based Maintenance (CBM)
CBM uses sensor data to monitor asset health. When performance indicators drop (e.g., vibration, heat, pressure), the software automatically schedules maintenance.
Example: If a machine starts vibrating beyond a set limit, the system alerts a technician before a breakdown occurs.
Predictive Maintenance (PdM)
This approach goes a step further—using AI and machine learning to forecast failures. PdM identifies patterns in usage, failure history, and sensor data to predict problems before they happen.
Benefits of CBM & PdM with Preventive Maintenance Software:
- Lower Repair Costs
- Fewer Unnecessary Inspections
- Minimal Downtime
- Optimized Part Replacement Cycles
These advanced strategies are becoming more accessible as IoT adoption grows. Modern PMS platforms like UpKeep and Fiix now offer condition-based modules, making predictive maintenance a viable upgrade for many businesses.
Discover great ideas like reliability-centered maintenance to combine these models for a hybrid approach that maximizes ROI.
Top Preventive Maintenance Software Tools in 2025
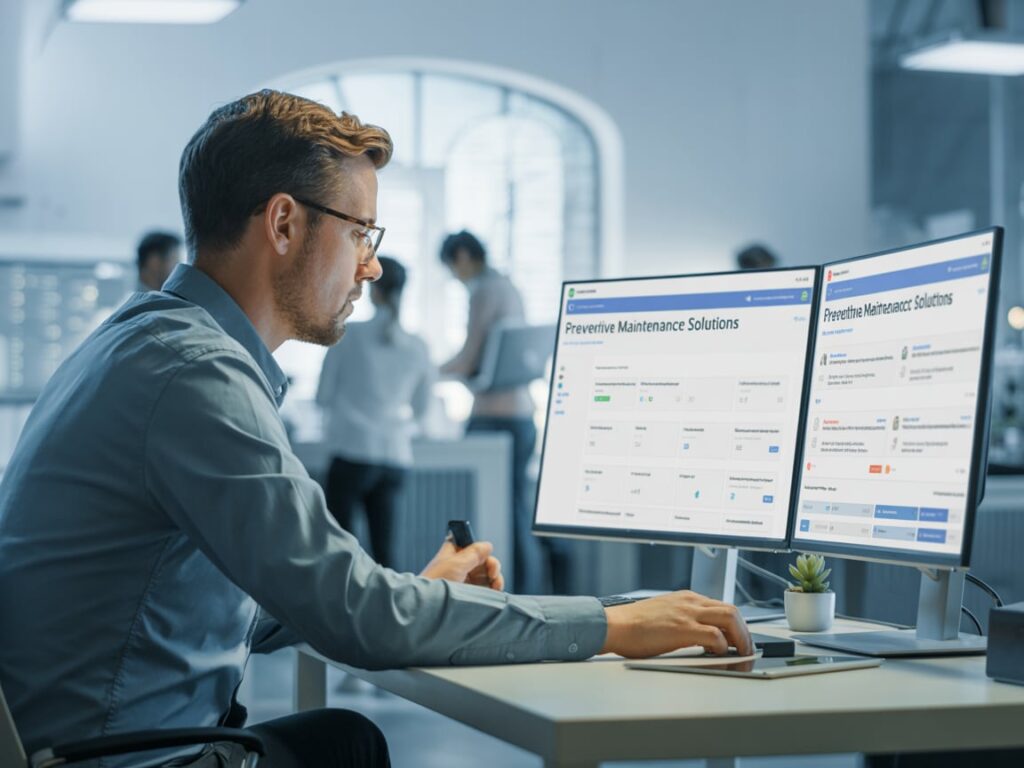
Review of the Best PMS Software for Different Industries
In 2025, the preventive maintenance software market is more competitive than ever. From manufacturing floors to commercial fleets and even residential property management, businesses are looking for the best PMS (Preventive Maintenance Software) to streamline operations.
Below is a curated list of the most reliable platforms based on usability, industry focus, integrations, and support:
Software | Best For | Key Features | Pricing |
---|---|---|---|
UpKeep | SMBs, Facilities, Property Managers | Mobile-first, Work Order Automation, QR Code Scanning | Starts at $45/month |
Fiix | Manufacturers, Large Facilities | AI-Driven Maintenance, Custom Dashboards, Open API | Starts at $60/month |
MaintainX | Frontline Teams, Multi-Site Businesses | Live Chat, Digital Forms, Asset Hierarchy | Starts at $49/month |
Hippo CMMS | Schools, Hospitals, Warehouses | Work Order Portal, Simple UI, Calendar View | Quote-based |
Limble CMMS | Maintenance Teams, Industrial | Asset Cards, Offline Mode, Vendor Management | From $40/month |
eMaint by Fluke | Enterprise Level Ops | CMMS + PdM Tools, Global Support, Modular Design | Custom plans |
All of these solutions allow you to automate scheduling, track maintenance histories, and manage assets efficiently. What sets them apart is industry alignment and user interface—something you should assess based on your unique needs.
Looking for inspiration? Try our About page to see how Sam’s philosophy of simplicity and real-world utility influences even software selection.
Comparing Features, Usability, and Support
Here’s how these tools stack up against the must-have features of effective preventive maintenance platforms:
Feature | UpKeep | Fiix | MaintainX | Hippo | Limble | eMaint |
---|---|---|---|---|---|---|
Mobile App | ✅ | ✅ | ✅ | ✅ | ✅ | ✅ |
Predictive Maintenance | ❌ | ✅ | ❌ | ❌ | ✅ | ✅ |
Custom Reports | ✅ | ✅ | ✅ | ✅ | ✅ | ✅ |
IoT Integration | ❌ | ✅ | ❌ | ❌ | ✅ | ✅ |
Work Order Management | ✅ | ✅ | ✅ | ✅ | ✅ | ✅ |
Offline Access | ✅ | ❌ | ✅ | ❌ | ✅ | ✅ |
User Feedback & Support:
- UpKeep is praised for being beginner-friendly and mobile-ready.
- Fiix offers great customization but may require a learning curve.
- MaintainX wins in real-time collaboration features.
- Hippo is easy to train new users on, especially in healthcare and education.
- Limble delivers an intuitive UI with strong offline capabilities.
- eMaint is the go-to for enterprises needing scalable, global solutions.
Check out our real-world maintenance workflows to see how these platforms support everyday tasks like fleet upkeep.
If you’re just starting or managing a small setup, even a basic tool with strong scheduling features can deliver major returns.
Don’t miss our post on reliability-centered maintenance, which works hand-in-hand with these systems to reduce asset failure across all industries.
Preventive Maintenance Software vs. Excel and Manual Systems
Why Excel Isn’t a Scalable CMMS Tool
While Excel spreadsheets are often the starting point for small businesses or DIYers managing maintenance schedules, they quickly fall short when operations grow. Many teams mistakenly treat Excel as a CMMS (Computerized Maintenance Management System), but the limitations become clear fast.
Let’s break down why Excel is not a scalable alternative to preventive maintenance software:
Feature | Excel | Preventive Maintenance Software |
---|---|---|
Automation | ❌ Manual updates | ✅ Auto task creation, reminders |
Collaboration | ❌ Versioning issues, no live sync | ✅ Real-time updates, multi-user |
Mobile Access | ❌ Not mobile-optimized | ✅ Dedicated mobile apps |
Asset Tracking | ❌ No history logs | ✅ Maintenance logs, part tracking |
Reporting | ❌ Requires manual setup | ✅ Built-in analytics, dashboards |
Here’s the biggest issue: data reliability. One mistake in a spreadsheet—like a missed formula or outdated task status—can cause critical maintenance to be skipped. Over time, this leads to asset damage, costly repairs, or even safety risks.
And let’s not forget version control nightmares. If multiple team members are working in separate spreadsheet copies, it’s easy to lose track of real-time updates. You might be fixing a machine that someone already serviced—just because the document wasn’t synced.
Discover great ideas like reliability-centered maintenance that rely on real-time data accuracy—something spreadsheets can’t deliver.
Transitioning from Spreadsheets to Automated Solutions
Switching from Excel to preventive maintenance software might seem overwhelming at first—but it’s one of the most valuable upgrades your team can make.
Here’s how to ease the transition:
- Audit Existing Data: Clean up your Excel records—remove duplicates, confirm equipment IDs, and organize service dates.
- Choose the Right Platform: Identify your needs—budget, features, industry focus—and test 2–3 top tools.
- Import Existing Data: Most modern software solutions allow CSV import of asset lists and maintenance logs.
- Train Your Team: Run a short onboarding session to show how to create work orders, close tasks, and view reports.
- Start Small: Don’t migrate every asset immediately. Start with one site or system, and scale once comfortable.
Looking for inspiration? Try our About page to see how our founder started with paper checklists and built a practical system designed to grow with your needs.
UpKeep, Fiix, and MaintainX all offer onboarding support and knowledge bases to help teams ditch outdated spreadsheets and move into streamlined, centralized maintenance.
Still on Excel? You’re not alone—but now’s the time to upgrade. Check out this beginner-friendly guide to learn how digital scheduling has transformed daily workflows across industries.
How to Choose the Best Preventive Maintenance Software
Key Considerations: Budget, Features, Industry Needs
Choosing the right preventive maintenance software isn’t about finding the most expensive or the most feature-rich option. It’s about matching the tool to your unique operational needs.
Here are the critical factors to evaluate:
- Your Industry Type
Different industries have different needs. For example:- Manufacturing needs asset-intensive tracking and predictive analytics
- Facility management often relies on work order automation and mobile apps
- Fleet operators require mileage-based scheduling and inspection logs
Explore real-world strategies in our truck maintenance case study to understand the nuances of a fleet-first system.
- Asset Volume and Complexity
Are you managing 10 HVAC units or 1000 production machines?
The higher the volume and variety, the more you’ll benefit from features like asset hierarchies, barcode scanning, and parts inventory. - Team Size and Mobility
If your technicians are constantly moving between job sites, look for mobile-first platforms like UpKeep or MaintainX. - Budget and Growth Plan
Entry-level platforms start around $35–$45/month per user. But enterprise-grade tools like eMaint require custom quotes.
Don’t overpay for features you won’t use—but don’t underinvest if scalability is a goal. - Integration Needs
Will the software need to connect with your accounting system? ERP platform? IoT sensors?
Look for APIs, Zapier support, or native integrations that match your digital ecosystem.
Tip: Most top-tier software platforms offer a free trial. Always test the platform with your actual data and team before committing.
Discover great ideas like reliability-centered maintenance—a strategic model you may want to integrate as your software scales.
Questions to Ask Vendors Before Making a Purchase
When comparing options, go beyond features. These key questions can help clarify which vendor is right for you:
- What onboarding support do you provide?
Is there training, a knowledge base, or a setup concierge? - Can the software handle my specific asset types and schedules?
Look for demos that show how it works for your industry. - Is mobile access included or charged separately?
Some platforms charge extra for mobile users or app access. - What’s your average response time for support tickets?
Reliable support is non-negotiable for mission-critical operations. - Do you support predictive maintenance integrations?
If you plan to grow into AI-based solutions, ask if they support IoT inputs. - Can I export and back up my data easily?
You want to own your records—not get locked into a platform with limited export capabilities.
Looking for inspiration? Try our About page to understand how simple, effective planning (not perfection) leads to long-term success in every maintenance system.
Implementing Preventive Maintenance Software Effectively
Planning, Data Migration, and Staff Training Tips
Implementing preventive maintenance software the right way is just as important as choosing the right one. Rushing the rollout—or skipping key planning steps—can lead to confusion, poor adoption, and wasted investment.
Here’s how to do it right:
1. Build an Implementation Plan
Before anything else, map out:
- Key objectives (e.g., reduce downtime by 20%, automate 100% of HVAC tasks)
- Timeline and rollout phases
- Team members responsible for each step
Tip: Start with one department, site, or asset type. Then scale once your team feels comfortable.
2. Audit and Clean Existing Data
This step can’t be skipped.
- Remove duplicate assets
- Confirm serial numbers and service records
- Identify missing warranty info, location details, and service vendors
This ensures accurate scheduling and reporting once imported into the system.
3. Migrate Data Strategically
Most software platforms offer:
- CSV import for bulk asset uploads
- Mapping support to align your Excel columns with software fields
- Migration services (often free with annual plans)
Upload a clean version of your current data. Verify it’s displaying correctly. Don’t forget to add images, manuals, and warranty documents to each asset card.
4. Train Your Team Early and Often
People resist change—especially if it complicates their day. You’ll want to:
- Create clear cheat sheets or process guides
- Host hands-on training sessions with your actual equipment
- Highlight how the software helps them: easier inspections, mobile checklists, fewer follow-ups
Looking for a real-world example of system rollout? Don’t miss our guide to truck preventive maintenance—it includes the rollout of software for vehicle inspections and mileage logs.
5. Test, Tweak, Then Scale
Start with a pilot group—maybe just HVAC systems or a single team—and observe how they interact with the platform. Track:
- Are tasks being closed on time?
- Are work orders being logged properly?
- Are any assets missing key details?
Use feedback to adjust workflows, task descriptions, and asset groupings before scaling organization-wide.
Common Implementation Mistakes to Avoid
Avoid these frequent pitfalls that slow down adoption and reduce software ROI:
- Skipping the pilot phase: Jumping into full rollout without testing can lead to chaos.
- Importing messy or outdated data: “Garbage in, garbage out.” Always clean first.
- Failing to set user permissions: Letting everyone edit all tasks and assets = data loss risk.
- Neglecting mobile usability: Your techs will resist if it’s hard to use on the job.
- Not aligning with maintenance goals: Don’t just “set and forget.” Use the software to actually track KPIs like downtime, asset costs, and completion rates.
Looking for inspiration? Read about Sam’s journey on our About page, where maintenance became a daily mindset rooted in clarity, care, and consistency.
Future of Preventive Maintenance Software and Smart Tools
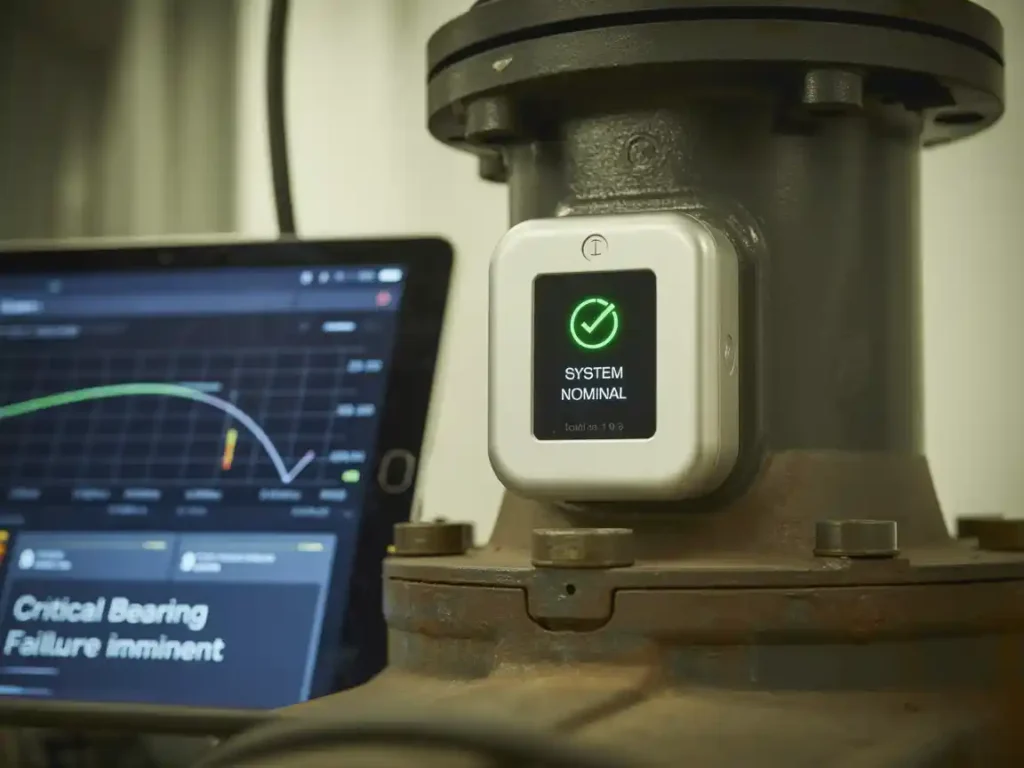
Role of AI, IoT, and Mobile in Maintenance Management
As we look ahead, preventive maintenance software is evolving beyond calendars and checklists. It’s becoming smarter, faster, and more autonomous—thanks to AI, IoT (Internet of Things), and mobile-first innovation.
Here’s how these technologies are shaping the future of maintenance:
Artificial Intelligence (AI)
AI is transforming how organizations interpret maintenance data. Today’s software can:
- Analyze asset performance and predict breakdowns
- Recommend ideal maintenance intervals
- Flag recurring issues with automatic root cause analysis
Instead of reacting to problems, AI helps organizations take preemptive action based on patterns across all equipment—something Excel or manual tracking could never achieve.
IoT Integration
IoT sensors can now monitor asset conditions in real time. Temperature, vibration, pressure, oil levels—you name it.
These sensors trigger tasks in your preventive maintenance software automatically, creating a fully hands-off scheduling process that responds to machine health rather than guesswork.
Example: When a boiler’s pressure reading spikes, the system logs the anomaly, assigns a task, and notifies the technician—all without human intervention.
Mobile-First Access
With most technicians now relying on smartphones and tablets in the field, mobile access is no longer optional. The best platforms offer:
- Barcode scanning to instantly identify assets
- Mobile forms for quick inspection reports
- Push notifications for task updates
- Offline access for areas with no connectivity
This increases completion rates, reduces downtime, and gives managers instant visibility into field activity.
Want to see how preventive maintenance evolves in the real world? Learn more about mobile-friendly strategies in our truck preventive maintenance workflow.
Upcoming Trends and Innovations in PMS Platforms
Here’s a glimpse at where preventive maintenance software is headed:
- Digital Twins: Creating virtual models of physical assets to simulate performance and maintenance needs.
- Voice-Enabled Work Orders: Using voice commands to update or close tasks—ideal for hands-busy environments.
- Augmented Reality (AR): Providing on-screen visual instructions for maintenance, layered over real-world assets via mobile camera.
- Unified Asset Platforms: Combining preventive, predictive, and reliability-centered tools into a single dashboard.
- Carbon Footprint Tracking: Integrating ESG (Environmental, Social, Governance) metrics to track energy use and sustainability impact from equipment.
These technologies will redefine what it means to “maintain” equipment. Companies that embrace automation and data-driven decision-making now will gain a competitive edge in efficiency, reliability, and cost savings.
Looking for inspiration? Try our About page—it all started with a handwritten checklist and a mindset focused on prevention.
Frequently Asked Questions About Preventive Maintenance Software
What is preventative maintenance software?
Preventive maintenance software is a digital tool that helps organizations and individuals schedule, track, and manage recurring maintenance tasks. It ensures assets and equipment are serviced before failures occur, reducing downtime and extending the life of machines, systems, or infrastructure.
What are the 4 types of software maintenance?
The four main types of software maintenance are:
Corrective Maintenance – Fixing bugs and errors
Preventive Maintenance – Updating software to avoid future problems
Perfective Maintenance – Enhancing performance or features
Adaptive Maintenance – Modifying software to work in new environments (e.g., OS upgrades)
What is preventive maintenance tools in software?
Preventive maintenance tools in software include modules like:
Task schedulers for recurring services
Asset trackers for maintenance history
Inventory managers to monitor spare parts
Reporting dashboards for performance analytics
These tools automate routine maintenance, reduce errors, and keep systems operating at peak efficiency.
What is the best maintenance software?
There’s no one-size-fits-all solution. However, based on usability and features:
UpKeep is best for small to mid-sized businesses.
Fiix offers strong AI and reporting tools for manufacturers.
MaintainX excels in mobile-first task management.
Each platform fits different industries and needs. Learn more in our comparison in Part 5.
What is the best PMS software?
The best PMS (Preventive Maintenance Software) in 2025 includes:
UpKeep for intuitive mobile access
Limble CMMS for robust asset management
eMaint for enterprise-level integrations
Your choice should align with your asset volume, mobile needs, and industry compliance.
Is Excel a CMMS?
No, Excel is not a CMMS. While it can be used for basic tracking, it lacks automation, collaboration tools, and real-time analytics that a preventive maintenance software or CMMS provides. Excel is prone to data errors and doesn’t scale for growing operations.
Conclusion: Best Preventive Maintenance Software
Preventive maintenance software isn’t just for large factories or complex facilities—it’s a necessity for anyone who values efficiency, reliability, and peace of mind. Whether you’re overseeing a facility, managing a fleet, or just trying to stay on top of your home’s maintenance routine, the right software can transform how you work.
By shifting from reactive chaos to proactive control, you’re not only protecting your assets—you’re building a sustainable, smarter system for the future.
Don’t miss our full breakdown of reliability-centered maintenance to complement your software strategy and optimize long-term performance.