Pre-emptive maintenance isn’t just a buzzword—it’s a mindset rooted in care, consistency, and real-world problem solving. At UpkeepRecord.com, founder Sam built a resource-driven space inspired by early memories of her dad’s weekend repairs and her mom’s hyper-organized routine. She understood that the backbone of a safe, efficient life isn’t perfection—it’s proactive attention to the small stuff before it snowballs into costly issues.
That’s where pre-emptive maintenance comes in. It’s about being one step ahead—addressing risks before they become failures, protecting your assets through foresight, and making upkeep feel empowering, not exhausting. Whether you’re dealing with a squeaky hinge, aging HVAC system, or vehicle that needs more than just seasonal checkups, this guide walks you through everything you need to know.
We’ll explore what makes pre-emptive maintenance different from preventive or predictive maintenance, the practical benefits for your tools, home, and systems, and how to put it into action with smart strategies and tech tools. You’ll also find insights drawn from real-life challenges, expert FAQs, and tips that work for busy people—just like you.
Check out our take on HVAC preventative maintenance to see how proactive planning delivers real results.
Table of Contents
Understanding Pre-Emptive Maintenance
What is Pre-Emptive Maintenance?
Pre-emptive maintenance refers to the process of addressing potential issues before they arise—essentially staying a step ahead of failure. It’s not just about scheduled checkups like preventive maintenance, and it’s not about waiting for data to detect wear like predictive maintenance. Instead, pre-emptive maintenance blends historical insight, expert judgment, and known failure patterns to act before there’s any visible sign of trouble.
Imagine you’ve owned a truck for five years. Even if it’s running smoothly, you already know from experience or manufacturer reports that the transmission tends to show problems around the 6-year mark. Rather than wait for the signs—or a warning light—you proactively replace or service it early. That’s the essence of pre-emptive action.
This type of maintenance typically involves:
- Replacing parts based on manufacturer lifespan, not just condition
- Upgrading components before wear signs appear
- Regularly reviewing logs to spot patterns of future failure
It is particularly valuable in environments where failure leads to high costs, safety risks, or production downtime—like in manufacturing, HVAC, logistics, and fleet operations.
How It Differs from Preventive and Predictive Maintenance
While all three approaches aim to reduce equipment breakdowns, they differ in timing, data usage, and strategy. Here’s a breakdown:
Maintenance Type | Based On | Timing | Tools Used | Goal |
---|---|---|---|---|
Pre-emptive | Known failure timelines, expert insights | Before signs show | Maintenance logs, manuals | Prevent early failures proactively |
Preventive | Regular intervals or time-based | Periodically | Schedules, calendars | Avoid wear and tear |
Predictive | Real-time condition monitoring | When data indicates | Sensors, IoT, condition monitoring tools | Intervene just before failure |
Pre-emptive maintenance is proactive but doesn’t necessarily require expensive data-gathering tools. It’s accessible, practical, and ideal for teams who rely more on experience and records than high-tech diagnostics.
Don’t miss our deep dive into preventive maintenance software to explore how digital tools support both scheduled and pre-emptive efforts.
Benefits of Pre-Emptive Maintenance Strategies
Reducing Equipment Downtime and Failures
One of the most immediate benefits of proactive maintenance is its power to drastically cut unexpected downtime. When machines fail without warning, operations can grind to a halt—often at the worst possible time. By taking action before wear or malfunction becomes visible, organizations avoid emergency shutdowns, expensive overnight repairs, and missed deadlines.
For instance, manufacturers often schedule early replacement of parts that are known to wear out around specific usage milestones, even if the equipment appears to be functioning correctly. This proactive mindset prevents cascading failures—where one worn part causes damage to another, amplifying costs and complexity.
In fleet management, pre-emptive strategies prevent breakdowns mid-route, boosting both efficiency and safety. Want to see how this works in transportation? Discover great ideas like our truck preventive maintenance guide to see it in action.
Other direct advantages include:
- Consistent performance under pressure
- Improved reliability across critical systems
- Greater uptime in revenue-generating equipment
- Avoidance of emergency service fees
Downtime isn’t just an inconvenience—it’s a bottom-line problem. Pre-emptive maintenance offers a solution that’s both smart and scalable.
Increasing Asset Lifespan and ROI
When you fix or replace components before they fail, you protect your overall asset from unnecessary wear. This directly extends its useful life. A well-maintained HVAC system, for instance, may last 20%–30% longer than one that’s only serviced after problems appear. And the savings aren’t just on parts—they show up in energy efficiency, reduced labor hours, and improved system consistency.
Here’s where Return on Investment (ROI) comes into play. hile proactive maintenance might seem like more work initially, it leads to:
- Fewer costly repairs over time
- Longer replacement intervals for major equipment
- Better resale or residual value for well-maintained assets
- Smoother audits or inspections with well-kept records
Check out our take on reliability-centered maintenance to see how asset performance and longevity go hand in hand with proactive strategies.
Implementing a pre-emptive maintenance routine is like compound interest for your equipment—it pays off exponentially with time.
Core Principles and Components of Pre-Emptive Maintenance
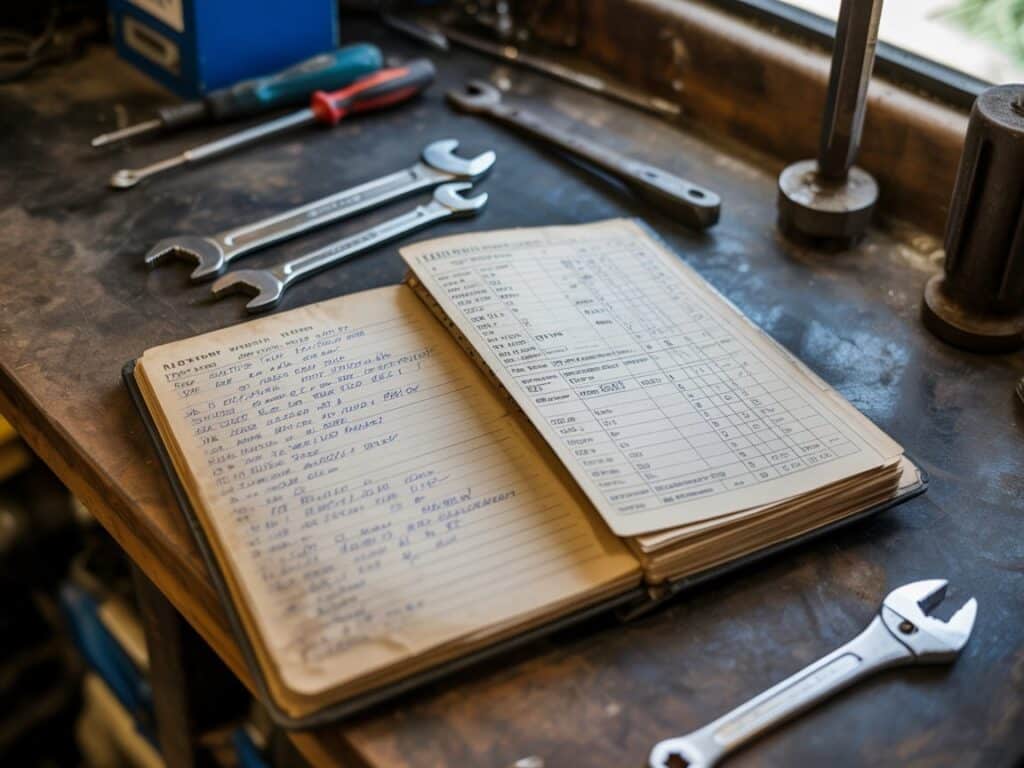
Data Monitoring and Real-Time Alerts
Even though pre-emptive maintenance doesn’t rely solely on high-tech tools like predictive maintenance, it still uses smart data as its foundation. One of its core principles is analyzing historical maintenance logs, usage trends, and known wear points to identify when issues are likely to occur.
Modern tools—even basic ones—can provide usage-based triggers and alerts based on:
- Operating hours
- Engine cycles
- Seasonal usage patterns
- Past failure trends
A simple spreadsheet or basic CMMS (Computerized Maintenance Management System) can offer insights like: “This pump has run 2,000 hours since its last seal replacement—time to swap it out early.” This proactive action prevents degradation before sensors ever flag a warning.
For teams with tighter budgets, this approach avoids over-reliance on sensors or costly IoT solutions while still offering valuable foresight.
Root Cause Analysis and Proactive Planning
Pre-emptive maintenance isn’t just about reacting—it’s about strategically planning for known risks. This involves a methodical look into:
- Why certain parts consistently fail
- How environmental factors (like heat or humidity) contribute
- Whether specific usage patterns trigger issues
By using Root Cause Analysis (RCA), maintenance teams can prioritize what needs attention first and create maintenance schedules that are smarter, not just busier.
Let’s say your HVAC system tends to overheat during summer peak usage. Instead of waiting for the next breakdown, you create a pre-summer checklist that targets known weak points—before they show symptoms. You don’t guess; you act based on experience and pattern recognition.
Planning includes:
- Parts procurement in advance
- Workforce scheduling
- Downtime optimization for replacements
- Aligning upgrades with production lulls
Looking for inspiration? Try our guide on hvac preventative maintenance to see how proactive scheduling helps prevent summer failures.
In essence, pre-emptive maintenance runs on a simple but powerful engine: anticipate, prepare, act early, and repeat.
Pre-Emptive vs. Preventive Maintenance: Key Differences
Definitions and Use-Cases Compared
At first glance, pre-emptive maintenance and preventive maintenance might seem interchangeable. After all, both aim to stop problems before they occur. But the difference lies in how and why they’re performed.
Feature | Pre-Emptive Maintenance | Preventive Maintenance |
---|---|---|
Trigger | Based on patterns, expert knowledge, and known risks | Based on fixed time intervals or usage cycles |
Flexibility | Highly adaptive to known weak points | Follows a rigid schedule regardless of condition |
Efficiency | Targets specific failure points ahead of time | Covers all systems equally, often over-maintaining |
Cost Control | Reduces waste by replacing only what’s at risk | May replace components too early or too late |
Tools Needed | Maintenance history, trend data, expert judgment | Basic logs and calendars |
A pre-emptive approach might, for example, dictate replacing a certain bolt every 18 months—even though it technically has a 24-month lifespan—because past failures have shown it weakens earlier in humid environments.
On the other hand, a preventive schedule might mandate replacing that bolt every two years across all assets, regardless of use or conditions. This could mean replacing some bolts too late and others too soon.
The key takeaway? Pre-emptive maintenance is more focused and informed, making it a smarter choice in high-risk or high-cost environments.
When to Use Pre-Emptive Over Preventive
Knowing when to adopt a pre-emptive strategy can make or break your maintenance efficiency. Here’s when it’s best to prioritize pre-emptive maintenance:
- Critical Systems: Where failure leads to safety hazards or major losses
- Recurring Issues: If past logs reveal predictable breakdown patterns
- Seasonal Operations: Where equipment is under stress in specific months
- Budget Constraints: When replacing the wrong part too early costs money
- Remote Assets: Where breakdowns result in long service delays or travel
For example, if you’re managing HVAC systems that must run without fail during heatwaves, pre-emptively changing out fan belts or capacitors in June—even if they appear “okay”—prevents mid-July breakdowns.
Don’t miss our insights on preventive maintenance software, which can also support pre-emptive strategies with better data and flexible scheduling.
In short, use preventive maintenance for broad, routine care. Use pre-emptive maintenance when you need precision, reliability, and peace of mind based on experience.
Types of Maintenance and Where Pre-Emptive Fits
Overview of the 4 Main Types of Maintenance
To truly understand where pre-emptive maintenance fits into the broader picture, it’s essential to break down the four foundational maintenance types. Each serves a distinct purpose, but only pre-emptive and predictive take a forward-thinking approach to failure prevention.
Type | Description | Timing | Example |
---|---|---|---|
Corrective Maintenance | Action taken after a failure occurs | After failure | Replacing a blown HVAC capacitor |
Preventive Maintenance | Scheduled upkeep based on time or usage | Before failure | Oil change every 5,000 miles |
Predictive Maintenance | Condition-based maintenance triggered by sensor data | At risk threshold | Replacing a motor after vibration level spikes |
Pre-Emptive Maintenance | Risk-based replacement before any visible issue based on known trends | Before symptoms | Replacing parts early based on recurring failure |
What makes pre-emptive maintenance unique is that it combines proactive timing with human insight. It doesn’t rely heavily on sensor data like predictive maintenance, nor does it follow rigid time schedules like preventive maintenance.
It thrives on:
- Maintenance logs
- Manufacturer alerts
- Past breakdown reports
- Equipment usage trends
- Environmental influences (e.g., heat, moisture)
Pre-emptive maintenance is strategic, not static.
Situational Applications of Pre-Emptive Maintenance
Depending on the industry or asset type, pre-emptive tactics may be essential—or even mandatory. Below are scenarios where this maintenance style becomes the most efficient and reliable choice:
1. Manufacturing Plants
Production equipment, especially in high-speed operations, benefits greatly from early part replacements. For example, rollers known to warp after 500 hours of use may be replaced at 450 hours to avoid unexpected jams.
2. HVAC Systems
In climates with harsh summers or winters, replacing known-failure-prone components like fan belts or filters before seasonal spikes keeps homes and buildings comfortable without interruption.
3. Logistics and Transportation
Fleet managers often pre-emptively change tires, fluids, and brake components before long hauls—especially when previous trips showed deterioration near specific mileage markers.
4. Food & Pharma Processing
These sectors cannot afford surprise downtime. Pre-emptive part swaps ensure compliance and continuous production, especially during peak regulatory periods.
In each of these cases, the cost of preparing early is far less than the cost of reacting late.
How to Implement a Pre-Emptive Maintenance Plan
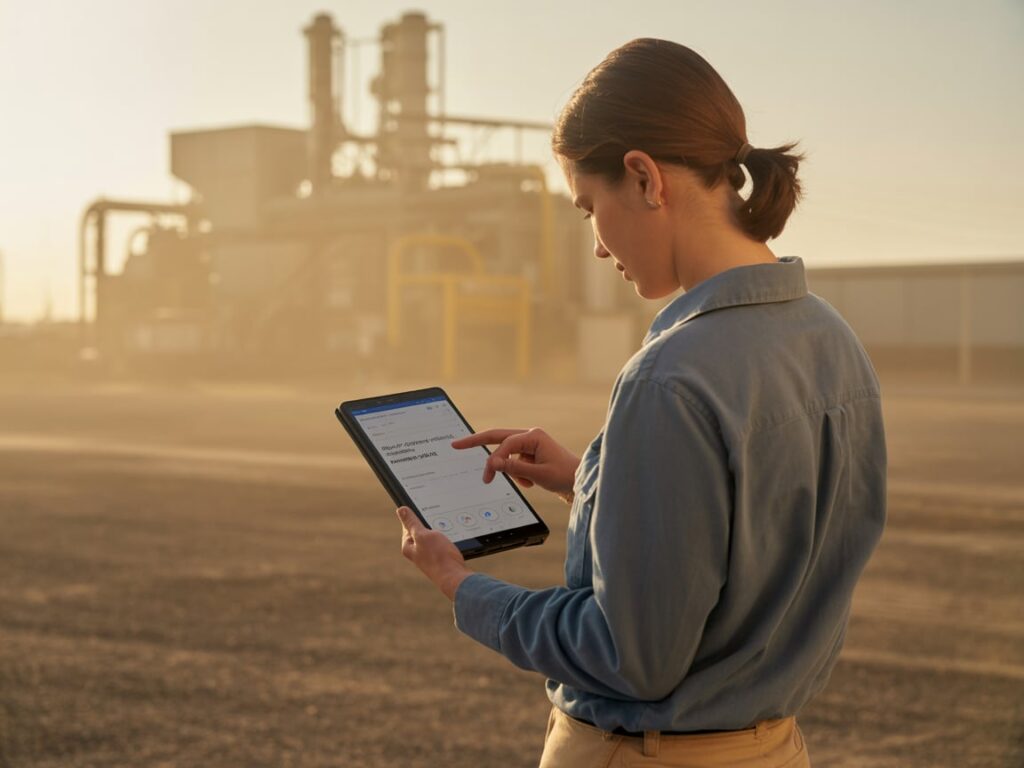
Step-by-Step Implementation Framework
Implementing a pre-emptive maintenance strategy doesn’t require an overhaul of your entire system—but it does demand a shift in mindset. Rather than waiting for issues or relying strictly on a fixed calendar, you begin managing risk and replacing parts before failure.
Here’s a proven step-by-step framework:
1. Review Past Failures and Work Orders
Start by gathering maintenance logs, service records, and incident reports. Identify recurring failures and note when they typically occurred relative to asset age or usage. Patterns will emerge, giving you insight into what needs early attention.
2. Identify High-Risk Equipment
Prioritize equipment that is:
- Mission-critical to your operation
- Expensive to repair or replace
- Prone to historical failure
Focus your pre-emptive efforts where breakdowns are the most costly.
3. Build Risk-Based Maintenance Intervals
Rather than using a flat schedule (e.g., change filter every 90 days), adjust timelines based on environmental factors and usage. For instance, if compressors in dusty environments fail at 14 months, set a 12-month pre-emptive replacement schedule.
4. Use Simple Tracking Tools or CMMS
A CMMS (Computerized Maintenance Management System) like the ones covered in our guide on preventive maintenance software can help track triggers, usage metrics, and auto-generate alerts when assets hit risk zones.
5. Assign Tasks and Schedule Replacements
Schedule pre-emptive tasks during low-demand periods to avoid business interruption. Keep your team in the loop and use task automation to stay consistent.
6. Document and Adjust
Every action should be logged. Over time, adjust intervals based on actual results—if parts are being replaced too early, or if failures still sneak through, refine your plan accordingly.
7. Educate and Empower Your Team
Train your staff to recognize risk indicators and respect the logic behind early replacement. Maintenance culture is key to long-term success.
Common Pitfalls and How to Avoid Them
Even with a solid strategy, several mistakes can slow or sabotage your success. Here are the biggest pitfalls—and how to steer clear:
1. Replacing Everything Too Early
Pre-emptive doesn’t mean premature. Use evidence, not fear, to guide replacements. Over-maintaining leads to waste.
2. Ignoring Frontline Input
Technicians often notice early signs of wear before data reflects it. Ignoring their input can cause preventable failures.
3. Failing to Document Work
Skipping documentation makes it impossible to improve. Every early replacement should be logged for future reference.
4. Not Factoring in Environment
One-size-fits-all doesn’t work. Dust, humidity, heat, and vibration all affect asset lifespan. Adjust your schedule accordingly.
5. Relying Only on Gut Feelings
Experience matters, but combine it with logs and data. The most powerful approach blends logic with history.
Want to streamline your process? Check out tools we recommend in our reliability-centered maintenance breakdown to help centralize data and decision-making.
Tools and Software for Pre-Emptive Maintenance
Features to Look for in Pre-Emptive Maintenance Software
While pre-emptive maintenance can begin with pen-and-paper or Excel sheets, scaling your strategy requires tools that simplify scheduling, tracking, and decision-making. Not all maintenance software is designed for pre-emptive logic, so knowing what to look for is key.
Here are the essential features your software should provide:
1. Customizable Scheduling
You should be able to set flexible service intervals based on usage, environmental conditions, or known failure patterns—not just fixed timelines.
2. Maintenance History Logs
The software must track all past service, component replacements, and technician notes. This data is crucial for identifying recurring issues and planning early interventions.
3. Risk-Based Work Order Automation
Look for platforms that allow for conditional triggers—like generating a work order if a component hits 80% of its typical failure point.
4. Integration with Parts Inventory
Pre-emptive maintenance depends on early preparation. Having real-time inventory tracking helps ensure parts are in stock when early replacements are scheduled.
5. Alerts & Notifications
Automated alerts prevent missed tasks and reduce human error. Alerts should be tied to conditions, usage milestones, or calendar dates—whichever is more relevant to the component.
6. Reporting & KPI Dashboards
The best tools allow you to monitor asset health, downtime reduction, cost savings, and maintenance backlog in one place. This helps justify your pre-emptive investments to stakeholders.
7. Mobile Access
Technicians in the field need real-time access to instructions, manuals, and checklists. Cloud-based platforms with mobile apps boost field efficiency and compliance.
Top-Rated Platforms and Technologies
If you’re just starting or scaling up your maintenance operations, consider the following popular CMMS and EAM tools that support pre-emptive maintenance logic:
Software | Best For | Pre-Emptive Features |
---|---|---|
UpKeep | Small to mid-sized teams | Mobile-first platform with strong scheduling and history tracking |
Fiix by Rockwell | Industrial operations | Risk-based triggers, asset logs, and predictive integration |
Hippo CMMS | Facility maintenance | Custom task automation and calendar-based early alerts |
MaintainX | Mobile teams | Easy checklists, early work orders, and downtime logging |
Limble CMMS | All-in-one solution | Robust pre-emptive modules, parts tracking, and real-time dashboard |
These platforms not only reduce paperwork but also empower your team to execute proactive maintenance consistently and confidently.
Looking to upgrade your existing system? Don’t miss our guide to preventive maintenance software to find tools that blend both preventive and pre-emptive strategies for maximum reliability.
Industry Applications and Case Studies
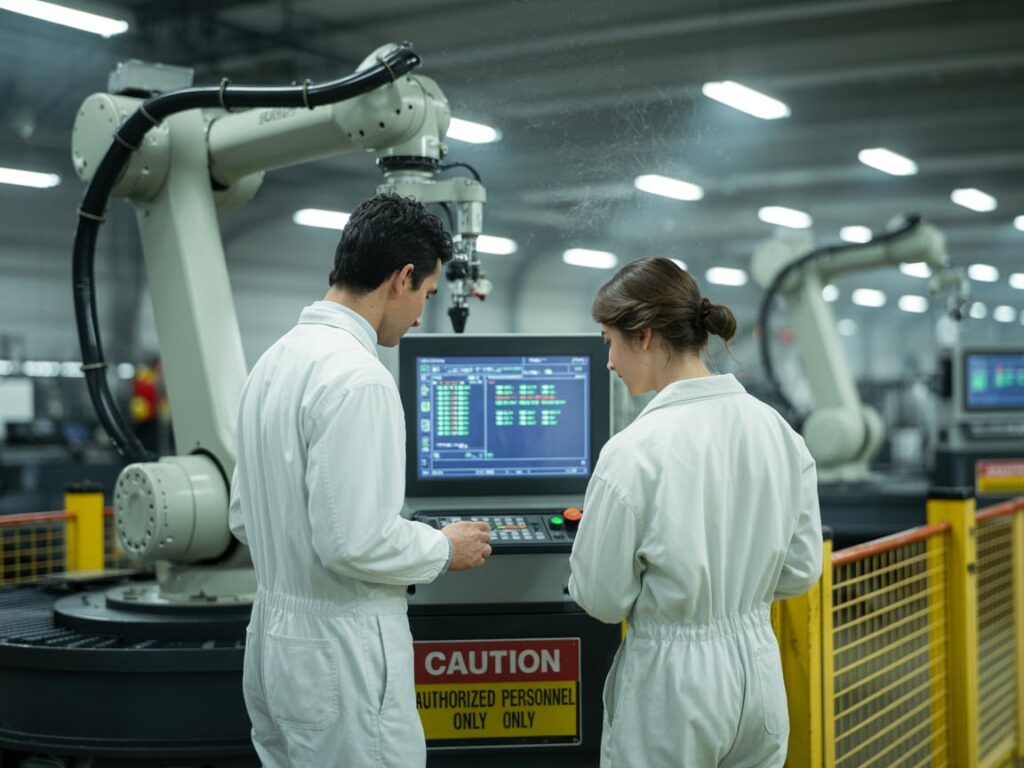
Manufacturing, Logistics, HVAC & More
Pre-emptive maintenance is adaptable across industries—anywhere equipment reliability is vital and unplanned downtime costs real money. Let’s explore how it plays out in key sectors:
1. Manufacturing
In high-speed production lines, even brief halts cost thousands in lost output. Pre-emptively replacing components like belts, bearings, and seals based on known wear patterns avoids chain-reaction breakdowns. Many plants use run-hour thresholds for parts with a history of early fatigue.
Case Example:
An electronics manufacturer began replacing conveyor motors after 1,800 hours of use—even though they were rated for 2,200 hours. Why? Because past logs showed failure rates spiked beyond 1,850 hours. The result? A 27% reduction in annual downtime and 15% savings in repair costs.
2. Logistics and Fleet Management
Vehicles in transit can’t afford roadside failures. Pre-emptive strategies include changing brake components, hoses, and tires based on mileage and environmental exposure (e.g., snowbelt corrosion). It’s also used for fuel injector replacement in trucks that show degradation at specific intervals.
Case Example:
A regional trucking company began replacing fuel injectors in delivery trucks every 95,000 miles instead of waiting until the standard 120,000. It eliminated over 30 unexpected repairs per year and kept delivery metrics above 98% on-time performance.
3. HVAC Systems and Building Maintenance
In facilities management, pre-emptive HVAC maintenance reduces tenant complaints, emergency call-outs, and seasonal system overload. It’s especially effective when applied to compressors, capacitors, and fan motors, which fail consistently in high-load conditions.
Want real-world ideas? Check out our full hvac preventative maintenance guide for a seasonal plan that works.
4. Food Processing and Pharmaceuticals
In regulated industries, a single equipment failure can halt production or trigger costly compliance audits. These industries rely heavily on pre-emptive change-outs of filters, sensors, and mixers—especially during peak demand or validation periods.
Case Example:
A dairy plant implemented early replacement of filling valves based on lab test data, cutting cross-contamination risk by 80% and increasing uptime by 20 hours per month.
Measurable Impacts in Real-World Scenarios
Pre-emptive maintenance might seem like an “extra” cost at first, but the ROI becomes crystal clear when you track results:
KPI | Before Pre-Emptive | After Implementation |
---|---|---|
Average Monthly Downtime | 18 hours | 6 hours |
Emergency Repair Costs | $12,000/month | $3,500/month |
Maintenance Overtime Hours | 45 hours/month | 12 hours/month |
Asset Life Expectancy | 7.8 years | 10.2 years |
These numbers show why forward-thinking operations embrace pre-emptive maintenance not as a cost—but as an investment.
Looking to apply this in your own operation? Don’t miss our breakdown of reliability-centered maintenance, a great framework for identifying high-risk components to tackle pre-emptively.
FAQs About Pre-Emptive Maintenance
What is pre-emptive maintenance?
Pre-emptive maintenance is a proactive maintenance strategy that involves replacing or servicing components before any signs of wear or failure appear. Unlike preventive maintenance, which follows a calendar or usage schedule, pre-emptive maintenance is based on historical failure data, expert insight, and operational risk. It’s used to prevent problems by acting before traditional warning signs emerge—ensuring higher reliability and reduced downtime.
What is preventive vs. preemptive?
Both preventive and pre-emptive maintenance are proactive, but they differ in timing and approach:
Preventive maintenance is performed at regular, predefined intervals (e.g., every 3 months or every 1,000 hours), regardless of asset condition.
Pre-emptive maintenance occurs before those intervals, based on expected failure patterns, real-world observations, or environmental conditions.
In short:
Preventive = Scheduled
Pre-emptive = Strategically early based on experience and risk
For example, if a part tends to fail at 2,000 hours, preventive maintenance might replace it at 1,800, while pre-emptive may replace it at 1,600 based on failure history in similar conditions.
What are the 4 types of maintenance?
The four main types of maintenance strategies are:
Corrective Maintenance – Performed after equipment breaks down.
Preventive Maintenance – Scheduled care to prevent breakdowns.
Predictive Maintenance – Data-driven maintenance based on asset condition and sensor alerts.
Pre-emptive Maintenance – Proactive maintenance based on known risk and historical failure data, performed before symptoms arise.
Each type has its role, but pre-emptive maintenance is ideal when failure is unacceptable and predictability is limited.
What is pred maintenance?
“Pred maintenance” is shorthand for predictive maintenance—a strategy that uses real-time data (via sensors, IoT, machine learning) to detect the exact moment a component begins to deteriorate. It enables highly efficient, condition-based interventions.
While predictive maintenance relies on technology, pre-emptive maintenance relies more on trend analysis and operational experience—making it easier to implement in low-tech or resource-constrained environments.
ChatGPT said:
Conclusion
Pre-emptive maintenance isn’t just another maintenance buzzword—it’s a smarter, data-informed approach to preventing costly downtime and extending asset life. By analyzing patterns, acting before symptoms arise, and scheduling replacements based on risk—not just time—you stay in control of your operations.
Whether you’re managing a fleet of trucks, maintaining an HVAC system, or overseeing a manufacturing plant, pre-emptive strategies deliver consistent reliability and peace of mind. They empower your team to act with confidence, cut waste, and optimize resources where they matter most.
At UpkeepRecord.com, we believe that maintenance should never be overwhelming. Our founder Sam’s mission is rooted in real-life experiences—where keeping things running isn’t about perfection, but about showing up early, staying ahead, and making maintenance manageable for everyday people.
Want to apply pre-emptive practices in your space?
Don’t miss our complete guide to truck preventive maintenance—it’s packed with insights to help you catch issues before they happen.
Together, let’s make breakdowns a thing of the past—one smart step at a time.