Reliability Centered Maintenance (RCM), Growing up, I watched my dad take on weekend repairs with confidence and my mom track every little task with a calendar full of reminders. That simple rhythm of care and consistency stuck with me. Years later, as a busy mom running a home and a digital space dedicated to smarter upkeep, I’ve learned something powerful: maintenance isn’t just about fixing what’s broken—it’s about preventing failure in the first place.
That’s where Reliability Centered Maintenance (RCM) comes in.
At UpkeepRecord.com, we’ve always been about making maintenance manageable for everyday people. Whether you’re tracking seasonal HVAC upkeep or diving deep into diagnostic tools, the goal remains the same—keep things running smoothly with minimal disruption. RCM is the professional-level strategy that takes that everyday logic and scales it up for complex systems like aircraft, manufacturing plants, and even high-performance IT infrastructure.
RCM asks the hard questions: What could go wrong? What are the consequences? And how can we stop it before it does? In this comprehensive guide, we’ll explore how Reliability Centered Maintenance can reshape the way you think about equipment care—by prioritizing critical functions, reducing unexpected breakdowns, and boosting your bottom line.
We’ll start with the basics, walk through each step of the RCM process, explore case studies from major industries, and even compare RCM to other common maintenance approaches. Along the way, you’ll find practical tools, real-world examples, and insight into how you can adopt RCM principles—no matter your level of experience.
Don’t miss our latest guide on proactive home maintenance to complement your technical RCM knowledge.
Let’s dive in.
Table of Contents
Understanding Reliability Centered Maintenance
What is Reliability Centered Maintenance (RCM)?
Reliability Centered Maintenance (RCM) is a strategic maintenance framework designed to ensure that physical systems continue to do what their users require in their current operating context. Unlike reactive or blanket preventive maintenance approaches, RCM focuses on identifying and prioritizing failure modes that could lead to significant operational disruptions or safety issues.
It was first developed by the aviation industry in the 1960s as a response to growing aircraft complexity. Traditional maintenance strategies weren’t enough—airlines needed a smarter, risk-based approach. Thus, RCM was born.
RCM asks seven key questions about each system component:
- What are its functions?
- In what ways can it fail?
- What causes each failure?
- What happens when it fails?
- How does it impact operations?
- What can be done to prevent or mitigate it?
- What happens if no maintenance is performed?
By answering these questions, you create a targeted, efficient maintenance plan tailored to the criticality and failure behavior of each asset.
This isn’t just theory—RCM principles are now standard in industries from manufacturing and oil & gas to power generation and transportation. They allow organizations to extend asset life, reduce downtime, and operate more safely and cost-effectively.
Looking for inspiration? Try this introductory guide on organizing your maintenance life through care and consistency.
Origin and History of RCM in Industrial Practices
The roots of Reliability Centered Maintenance (RCM) trace back to United Airlines and the U.S. Department of Defense in the late 1960s. As jet aircraft systems grew increasingly complex, mechanical failures became not only expensive but deadly. Engineers realized that fixed-schedule maintenance wasn’t enough—they needed something predictive, contextual, and based on real operational risks.
This realization led to the now-famous 1978 report titled Reliability Centered Maintenance, commissioned by the U.S. Department of Defense. The report laid out the framework for Reliability Centered Maintenance, emphasizing asset functionality, failure consequences, and tailored maintenance strategies designed to enhance system reliability.
Over time, Reliability Centered Maintenance expanded beyond aviation into commercial industries like power generation (especially nuclear) and manufacturing. By the early 2000s, major organizations such as Shell, NASA, and Boeing had adopted Reliability Centered Maintenance as a cornerstone of their preventive maintenance programs.
Today, modern Reliability Centered Maintenance is often integrated with digital solutions, including CMMS (Computerized Maintenance Management Systems). These platforms allow companies to track asset performance, predict equipment failures, and optimize resource use—making Reliability Centered Maintenance more effective and data-driven than ever before.
Why did RCM take off across industries?
Because it answers a universal need: How can we keep systems running with less failure, less waste, and more predictability?
And while the term may sound technical, its principles are deeply practical and transferable—whether you’re overseeing a multimillion-dollar asset fleet or just trying to extend the life of your home’s HVAC system.
📌 Internal Tip: Don’t miss our real-world tool recommendations for putting basic RCM concepts into practice at home.
Core Principles of Reliability Centered Maintenance
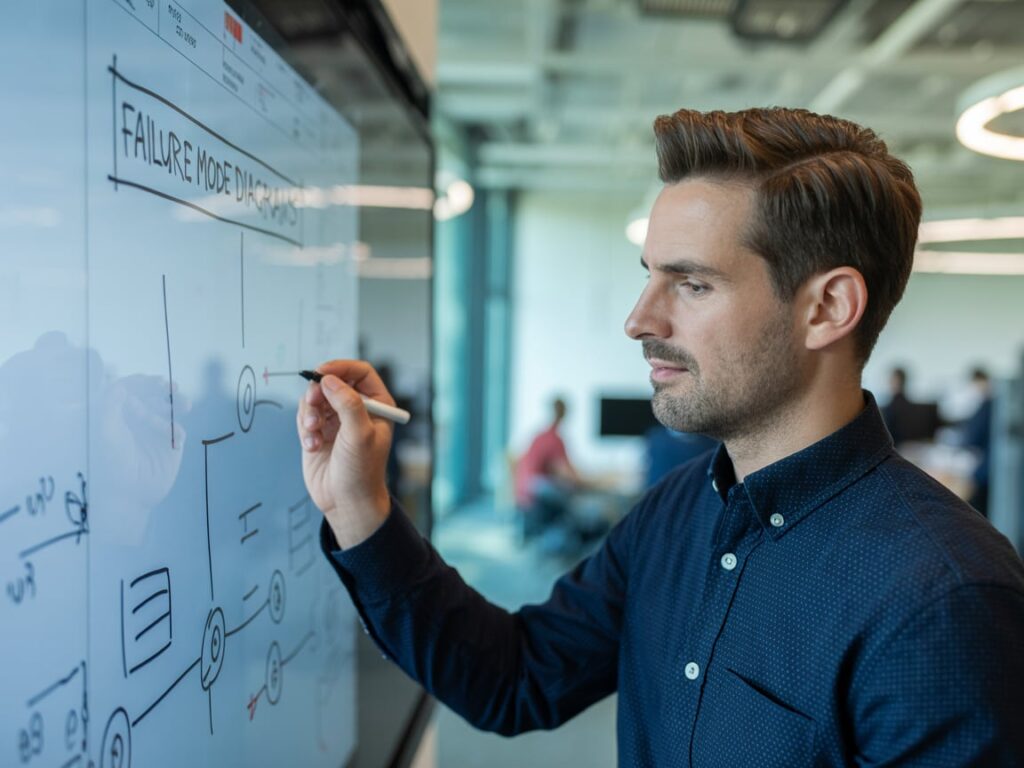
The 7 Key Questions of RCM Explained
At the core of Reliability Centered Maintenance (RCM) lies a structured, question-based methodology. These seven questions form the backbone of any RCM analysis, guiding teams through a logical process to develop a tailored maintenance strategy for each asset. Let’s break them down.
- What are the functions of the asset?
Begin by defining what the equipment is supposed to do—both its primary and secondary functions. For example, an HVAC unit’s primary function is to regulate temperature, but it may also dehumidify air or circulate ventilation. - In what ways can the asset fail to fulfill those functions?
These are your failure modes. Think leaks, wear-outs, software malfunctions, etc. Listing them helps anticipate what could go wrong. - What causes each functional failure?
This explores the root causes—corrosion, fatigue, human error, etc. Understanding failure triggers allows for smarter prevention. - What happens when each failure occurs?
Not all failures are catastrophic. Some might reduce performance; others could pose safety risks. The consequences help prioritize actions. - How does each failure affect the system or operation?
This focuses on operational impact—Will the system shut down? Will production slow? Will someone be hurt? Will regulations be violated? - What can be done to predict or prevent each failure?
Here, you define specific maintenance tasks—inspections, part replacements, lubrication—that reduce failure likelihood or detect early signs. - What happens if no action is taken?
Sometimes, it’s more efficient to let a failure occur if it’s low-impact or cheap to fix. This is called run-to-failure, and it’s a valid strategy for certain non-critical assets.
By systematically answering these questions, organizations develop a balanced maintenance strategy that combines preventive, predictive, and corrective tactics—minimizing risk while optimizing resources.
Discover great ideas like UpkeepRecord’s real-world checklists to apply a similar logic to everyday home systems.
Failure Modes and Effects Analysis (FMEA) in RCM
RCM doesn’t operate in isolation. It often leverages powerful tools like Failure Modes and Effects Analysis (FMEA) to dig deeper into how and why systems fail.
FMEA is a structured approach that:
- Identifies potential failure modes for components
- Evaluates the effect of each failure on the system
- Prioritizes risks based on severity, occurrence, and detection
Here’s a simplified example:
Component | Failure Mode | Effect | Severity | Occurrence | Detection | RPN (Risk Priority #) |
---|---|---|---|---|---|---|
HVAC motor | Bearings seize | Unit shuts down | 9 | 4 | 5 | 180 |
Air filter | Gets clogged | Poor airflow | 5 | 7 | 6 | 210 |
Thermostat | Malfunction | Temperature drifts | 6 | 3 | 5 | 90 |
Based on the RPN, teams can decide where to apply maintenance resources. In the example, even though motor failure is severe, a clogged filter is more likely and harder to detect, so it may require more frequent checks.
FMEA feeds directly into the RCM decision-making process by helping teams quantify risks and justify maintenance interventions.
So, why does this matter?
Because without a structured method like FMEA, you’re just guessing. And in high-stakes systems—like aircraft, medical equipment, or oil rigs—guessing leads to downtime, damage, and danger.
Don’t miss our upcoming guide on system failure analysis tools to pair with your RCM planning.
Benefits of Implementing RCM in Maintenance Strategy
Cost Savings and ROI Through RCM
One of the most compelling reasons to adopt Reliability Centered Maintenance (RCM) is its significant impact on cost efficiency. While traditional maintenance often relies on fixed schedules or reactive repairs, RCM strategically aligns maintenance tasks with asset criticality and actual risk—maximizing every maintenance dollar.
Here’s how RCM drives cost savings:
- Reduces Unplanned Downtime: Equipment failures don’t just cost money in repairs—they stall operations. RCM helps predict failures before they happen, avoiding the chaos and cost of surprise breakdowns.
- Prevents Over-Maintenance: Many companies throw resources at machines that don’t need it—replacing parts prematurely or inspecting too often. RCM cuts waste by only performing tasks when they’re truly needed.
- Improves Resource Allocation: With a clear picture of what assets are most critical, maintenance teams can prioritize time, parts, and budget where they’ll deliver the most value.
- Minimizes Inventory Costs: By focusing on failure modes, RCM helps reduce the need for stocking excessive spare parts—freeing up capital and storage.
Studies have shown that implementing RCM can reduce maintenance costs by 30–40% while simultaneously improving asset uptime. That’s a return worth investing in.
Check out UpkeepRecord’s home maintenance budget tips for more ways to apply cost-smart thinking to your own space.
How RCM Improves Asset Reliability and Uptime
At its core, RCM (Reliability Centered Maintenance) is about dependability. Whether you’re managing a factory floor or a fleet of service vehicles, you need your equipment to work when it’s supposed to. RCM delivers that by preventing failure, not just responding to it.
Here’s how RCM improves reliability:
- Targets Real Risk: RCM focuses on high-impact failures. Instead of spreading resources thin, it goes straight for the failures that matter most—keeping mission-critical systems running.
- Integrates Predictive Maintenance: RCM encourages the use of sensors, condition monitoring, and data analytics to catch early warning signs. This results in more precise, timely interventions.
- Extends Asset Lifespan: Preventing stress, wear, and major failures naturally prolongs the life of components and systems—delivering long-term savings and reducing capital expenditures.
- Improves Team Performance: Clear maintenance logic boosts confidence and consistency across teams. Everyone—from operators to planners—knows why a task is being done, which eliminates guesswork and increases accountability.
RCM isn’t a magic button—but when implemented thoughtfully, it becomes a long-term reliability engine.
Looking for more real-life wins? Don’t miss our seasonal equipment checklist strategies that work hand-in-hand with reliability-focused planning.
The RCM Process (Reliability Centered Maintenance): Step-by-Step Implementation Guide
Initial Assessment and Team Formation
Implementing Reliability Centered Maintenance (RCM) begins with the right people and the right preparation. While the process itself is structured and methodical, success depends heavily on cross-functional collaboration and a clear understanding of the systems at play.
Here’s how to start:
1. Identify the Asset or System to Analyze
Focus on high-impact systems—equipment whose failure would result in major safety risks, regulatory issues, or operational downtime.
2. Form a Dedicated RCM Team
A good RCM team includes:
- Maintenance experts
- Operators
- Engineers
- Safety personnel
- Quality or compliance reps
Each person brings unique insight into how the system behaves and what failure means.
3. Define the Scope and Objectives
Be clear: What’s the purpose of the Reliability Centered Maintenance study? Is it to reduce downtime? Improve safety? Meet compliance requirements? A narrow, well-defined scope ensures faster results and greater clarity.
4. Gather System Documentation
This includes equipment manuals, schematics, historical failure data, maintenance logs, and compliance checklists. The more informed your team is, the more accurate your analysis will be.
RCM isn’t just technical—it’s a culture of ownership and collaboration. Building the right team is your foundation.
Functional Failure Analysis and Task Selection
With the groundwork set, the RCM process moves into functional failure analysis (FFA)—where each asset is examined for how it can fail and what should be done about it.
Here’s a simplified process:
Step 1: Define Functions and Performance Standards
Clearly state what the equipment is supposed to do (primary and secondary functions). For instance, a water pump’s function is to deliver a set flow rate at a specific pressure.
Step 2: Identify Functional Failures
This is where we ask, “How can the pump fail to meet expectations?” Failures could include reduced flow, leakage, or total shutdown.
Step 3: Analyze Failure Modes and Effects
For each failure, identify:
- What caused it?
- What happens if it occurs?
- How does it impact the operation?
Use tables or diagrams (like FMEA charts) to visually organize this information.
Step 4: Prioritize Failure Modes
Use criteria like:
- Severity of consequence
- Frequency of failure
- Detectability
This helps determine which issues demand proactive attention.
Step 5: Select the Appropriate Maintenance Tasks
Now choose the best strategy for each failure:
- Preventive Maintenance (scheduled replacement or service)
- Predictive Maintenance (monitoring indicators like vibration or temperature)
- Detective Maintenance (inspections or functional checks)
- Run-to-Failure (intentional non-action for non-critical failures)
Each task must be technically feasible and worth doing—the cost of the task should not exceed the cost of failure.
Step 6: Document and Review
Record everything: chosen tasks, justifications, intervals, and who is responsible. Then review with stakeholders and adjust as needed.
Check out UpkeepRecord’s planning principles that help you organize and track these tasks in real-world environments.
📌 Table: Example of Functional Failure Breakdown
Component | Function | Failure Mode | Task Type | Interval |
---|---|---|---|---|
Air Compressor | Provide 90 PSI air supply | Pressure loss | Predictive | Continuous |
Control Valve | Regulate fluid flow | Stuck open | Preventive (replace) | Every 6 months |
Fan Motor | Maintain airflow | Bearing wear | Detective (inspect) | Monthly |
Light Fixture | Provide illumination | Bulb burnout | Run-to-Failure | N/A |
These examples show that Reliability Centered Maintenance (RCM) is not one-size-fits-all—each asset receives custom treatment based on failure consequence and cost-efficiency.
Don’t miss our DIY repair logic page for applying these same evaluation techniques to your home tools and systems.
Tools and Technologies Used in Reliability Centered Maintenance
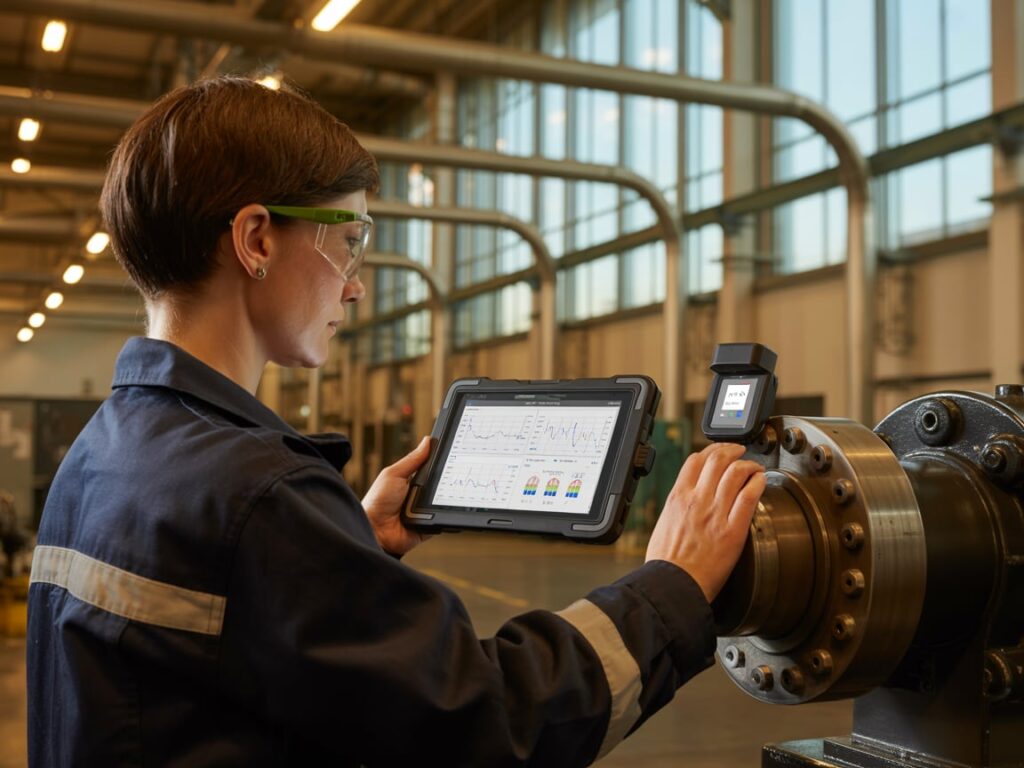
RCM Software Solutions and CMMS Integration
Modern Reliability Centered Maintenance (RCM) would be nearly impossible to implement effectively without the help of digital tools. From documenting failure modes to scheduling maintenance tasks, RCM relies heavily on Computerized Maintenance Management Systems (CMMS) and specialized RCM software.
Here’s how these tools support your Reliability Centered Maintenance (RCM) strategy:
1. Centralized Maintenance Data
CMMS platforms store:
- Equipment history
- Work orders
- Inspection results
- Performance logs
This centralized data enables teams to identify patterns and target high-risk areas—without guessing or flipping through paper logs.
2. Automated Task Scheduling
Once RCM identifies what needs to be done and when, CMMS automates task creation and notifications—ensuring nothing slips through the cracks.
3. Real-Time Reporting and KPIs
Track asset uptime, failure rates, Mean Time Between Failures (MTBF), and cost per asset—all key indicators to measure RCM effectiveness.
4. Integration with Sensors and IoT
Many platforms integrate with predictive maintenance technologies like vibration sensors or thermal imaging, allowing condition-based maintenance to be triggered in real time.
5. User Collaboration
From technicians to engineers, digital platforms streamline communication and task ownership—cutting down confusion and improving response time.
Popular RCM tools include:
- SAP PM
- IBM Maximo
- Fiix
- UpKeep
- Reliability Workbench
- RCM++ by ReliaSoft
If you’re a small business or homeowner, explore free or low-cost tools like UpKeep’s CMMS, which aligns well with our mission at UpkeepRecord.com to simplify proactive maintenance.
Predictive Maintenance and Condition Monitoring Tools
Predictive maintenance (PdM) is a core element of effective RCM. It involves monitoring equipment condition in real-time to predict failures before they happen—allowing interventions only when necessary.
Here are the most commonly used PdM technologies:
1. Vibration Analysis
Used heavily in rotating equipment like motors and pumps. Changes in vibration patterns signal wear, imbalance, or alignment issues.
2. Infrared Thermography
Detects heat variations in electrical panels, mechanical systems, or HVAC units. Hotspots often indicate overloaded circuits or bearing failure.
3. Ultrasound Detection
Useful for leak detection in compressed air systems and early warning signs in bearings.
4. Oil Analysis
Assesses contamination, viscosity, and wear particles in lubricated systems—offering insight into internal component condition.
5. Laser Alignment Tools
Ensure rotating shafts and pulleys are perfectly aligned, reducing stress and extending lifespan.
6. Internet of Things (IoT) Sensors
Sensors collect and transmit performance data continuously, enabling remote diagnostics and AI-driven maintenance decisions.
Tool | Application | RCM Role |
---|---|---|
Vibration Sensors | Pumps, fans, motors | Detect imbalance early |
Thermal Cameras | Electrical, mechanical equipment | Spot heat-related issues |
IoT Gateways | All connected assets | Real-time data + alerts |
Oil Test Kits | Gearboxes, compressors | Internal wear detection |
By combining these technologies with CMMS software, organizations achieve real-time asset intelligence—and that’s what RCM is all about.
Check out UpkeepRecord’s curated tools list for simpler, practical monitoring solutions for your home or small business.
Case Studies: Successful Applications of Reliability Centered Maintenance (RCM)
RCM in Aviation and Aerospace
The birthplace of Reliability Centered Maintenance (RCM) was the aviation industry—and for good reason. With passenger safety, compliance, and sky-high equipment costs at stake, airlines needed a smarter way to predict and prevent failures. Enter RCM.
Case Study: United Airlines
In the late 1960s, United Airlines pioneered the use of RCM to maintain its jet aircraft. Their traditional approach—replacing parts on a fixed schedule—wasn’t reducing failure rates. In fact, data showed many scheduled tasks had no real impact on performance.
RCM helped United Airlines:
- Identify critical failure modes like engine overheating and landing gear collapse
- Replace preventive overkill with condition-based inspections
- Cut maintenance costs while improving safety compliance
The result? Maintenance became more effective and efficient, and the U.S. Department of Defense quickly adopted the model.
NASA and the Space Shuttle
NASA implemented RCM for components aboard the Space Shuttle and International Space Station. Every failure mode was analyzed not just for mechanical risk, but also mission risk. When failure in space means a loss of life or mission, Reliability Centered Maintenance‘s structured approach becomes non-negotiable.
These high-reliability environments show that RCM is not just an engineering exercise—it’s a mindset of responsibility, risk-awareness, and operational excellence.
Reliability Centered Maintenance (RCM) in Manufacturing and Oil & Gas Industries
Beyond aviation, industries with continuous operations and tight margins have embraced RCM to maximize uptime and protect their assets.
Case Study: Shell Oil
Shell applied Reliability Centered Maintenance (RCM) across its refineries and offshore rigs. Their goals:
- Increase equipment uptime
- Improve worker safety
- Reduce unplanned shutdowns
Using Reliability Centered Maintenance (RCM), Shell:
- Identified which rotating equipment needed predictive monitoring
- Allowed non-critical equipment to run-to-failure, saving millions
- Prioritized safety-critical components for frequent checks
They reported a 30% reduction in equipment failures and 20% drop in total maintenance costs.
Case Study: Toyota Manufacturing
Toyota integrated RCM with its Lean practices to refine its Total Productive Maintenance (TPM) strategy. RCM helped:
- Target root causes of machine inefficiencies
- Improve OEE (Overall Equipment Effectiveness)
- Train operators to detect early signs of failure
With this approach, Toyota reduced downtime by over 25% and gained greater control over its maintenance KPIs.
Lessons Learned from Real-World Reliability Centered Maintenance (RCM)
Industry | Primary Benefit of RCM | Main Strategy Used |
---|---|---|
Aviation | Higher safety + reduced overhaul frequency | Predictive & scheduled tasks |
Oil & Gas | Less unplanned downtime, better cost control | Criticality-based prioritization |
Manufacturing | Higher efficiency + lower defect rates | Operator-led inspections |
Space/Aerospace | Mission-critical failure prevention | Full FMEA and risk-based planning |
These case studies reinforce a simple truth: RCM works wherever reliability matters most. And with the rise of automation, AI, and predictive tech, its impact is only growing.
Want to see how everyday maintenance strategy stacks up? Don’t miss our UpkeepRecord home maintenance frameworks built on similar principles.
Challenges and Limitations of Reliability Centered Maintenance (RCM)
Common Pitfalls During RCM Implementation
While Reliability Centered Maintenance (RCM) offers powerful benefits, it’s not without its challenges. Many organizations dive into RCM with high expectations, only to struggle with execution due to underestimating the scope and complexity.
Here are the most common pitfalls to watch out for:
1. Lack of Leadership Support
RCM demands time, collaboration, and budget. If upper management isn’t fully on board, the initiative often stalls. Without visible commitment, teams may deprioritize the process in favor of urgent tasks.
2. Incomplete Data or Poor Documentation
RCM relies on accurate failure history, asset specs, and performance data. If your systems are fragmented or missing records, the analysis becomes based on guesswork, not facts.
3. Overengineering the Process
Some teams get so caught up in analysis that they delay implementation. RCM isn’t about creating a perfect spreadsheet—it’s about taking smart, prioritized action.
4. Misidentifying Critical Equipment
Treating every asset as equally important spreads resources too thin. RCM’s effectiveness depends on correctly ranking equipment based on risk, impact, and cost of failure.
5. Poor Cross-Functional Collaboration
When maintenance, operations, and engineering work in silos, key insights are lost. RCM thrives on teamwork—without it, you miss critical viewpoints.
6. Failure to Review and Adjust
RCM is not “set it and forget it.” Assets evolve. Operating conditions change. Regular reviews are needed to keep the plan aligned with real-world demands.
Bottom line: RCM is a culture shift, not just a maintenance strategy. It requires buy-in, discipline, and continuous improvement.
Overcoming Resistance and Change Management in Teams
Shifting from reactive or time-based maintenance to a strategic, risk-informed model can stir up anxiety and resistance among teams. Operators may question its necessity. Technicians may worry about added workload. Managers may be skeptical of ROI.
Here’s how to manage change effectively:
1. Communicate the “Why” Clearly
Tie RCM directly to team goals—safety, efficiency, reduced downtime. Share real examples where poor maintenance led to costly consequences. People need to see the value.
2. Start Small with Quick Wins
Don’t try to roll out RCM across every system at once. Pick one high-impact asset, implement RCM thoroughly, and showcase the results. Early success builds momentum.
3. Train Your Teams
Host workshops, bring in experts, and give your staff the tools to understand and apply RCM. The more familiar they are, the less intimidating it feels.
4. Involve Frontline Workers Early
Your operators and technicians know your equipment best. When you involve them in the RCM process, you gain deeper insights—and greater buy-in.
5. Celebrate Progress
Track and share metrics: reduced downtime, fewer emergency repairs, improved asset life. Recognize teams for their role in making RCM a success.
6. Align with Broader Business Strategy
RCM works best when it supports broader organizational goals like quality improvement, regulatory compliance, and customer satisfaction. That alignment creates top-down and bottom-up support.
Looking for inspiration? Try UpkeepRecord’s simple repair and planning systems to show how consistency can ease change.
Reliability Centered Maintenance vs. Other Maintenance Strategies
RCM vs. Preventive Maintenance (PM)
Preventive Maintenance (PM) is a widely used strategy that involves scheduled maintenance tasks performed at fixed intervals—like changing oil every 5,000 miles or inspecting belts every 90 days. While PM is simple to implement and effective in many cases, it doesn’t consider real-world operating conditions or criticality.
Here’s how RCM compares to PM:
Factor | Preventive Maintenance (PM) | Reliability Centered Maintenance (RCM) |
---|---|---|
Basis | Time or usage intervals | Functional failure modes and risk |
Efficiency | Can lead to over-maintenance | Optimized to only what’s necessary |
Asset Criticality | Treats all assets similarly | Focuses on high-impact assets |
Data Required | Minimal | Detailed failure data and system knowledge |
Flexibility | Rigid schedules | Flexible and risk-driven |
Implementation Effort | Low to moderate | High (requires cross-functional analysis) |
RCM enhances preventive maintenance by applying it where it makes sense—and replacing it with predictive or conditional tasks where it doesn’t. It’s a smarter, data-driven upgrade to PM rather than a replacement.
Don’t miss our checklist system at UpkeepRecord for building preventive tasks that align with RCM principles.
RCM vs. Predictive and Reactive Maintenance
RCM vs. Predictive Maintenance (PdM)
Predictive Maintenance relies on sensor data and real-time monitoring to trigger maintenance only when signs of failure are detected—like vibration anomalies or thermal shifts. It reduces downtime and unnecessary work but requires tech investment.
Where it fits in with Reliability Centered Maintenance (RCM):
- PdM is often a tactic used within RCM
- RCM helps identify which assets deserve PdM treatment
- RCM defines what to monitor, how often, and what actions to take when data thresholds are crossed
RCM provides the strategic reasoning, while PdM provides the technical execution.
RCM vs. Reactive Maintenance
Reactive Maintenance, also known as “run-to-failure,” is the most basic form—only fix something after it breaks. While it works for non-critical assets like light bulbs or basic tools, it often leads to:
- High downtime costs
- Emergency repair fees
- Safety and compliance risks
RCM does allow run-to-failure—but only after careful evaluation that the consequences are acceptable.
Quick Comparison: Maintenance Strategy Roles in an Reliability Centered Maintenance (RCM) System
Maintenance Strategy | RCM Role |
---|---|
Preventive Maintenance | Used for wear-out failures with time patterns |
Predictive Maintenance | Used for hidden or sudden failures |
Reactive Maintenance | Applied to low-risk, low-cost failure modes |
Proactive Maintenance | Informed by RCM analysis to extend asset life |
RCM isn’t just another maintenance strategy—it’s a framework that tells you when and why to use each strategy. That’s what makes it uniquely powerful.
Looking for inspiration? Try UpkeepRecord’s seasonal guide to apply different maintenance strategies based on risk, timing, and asset criticality.
Future Trends in Reliability Centered Maintenance
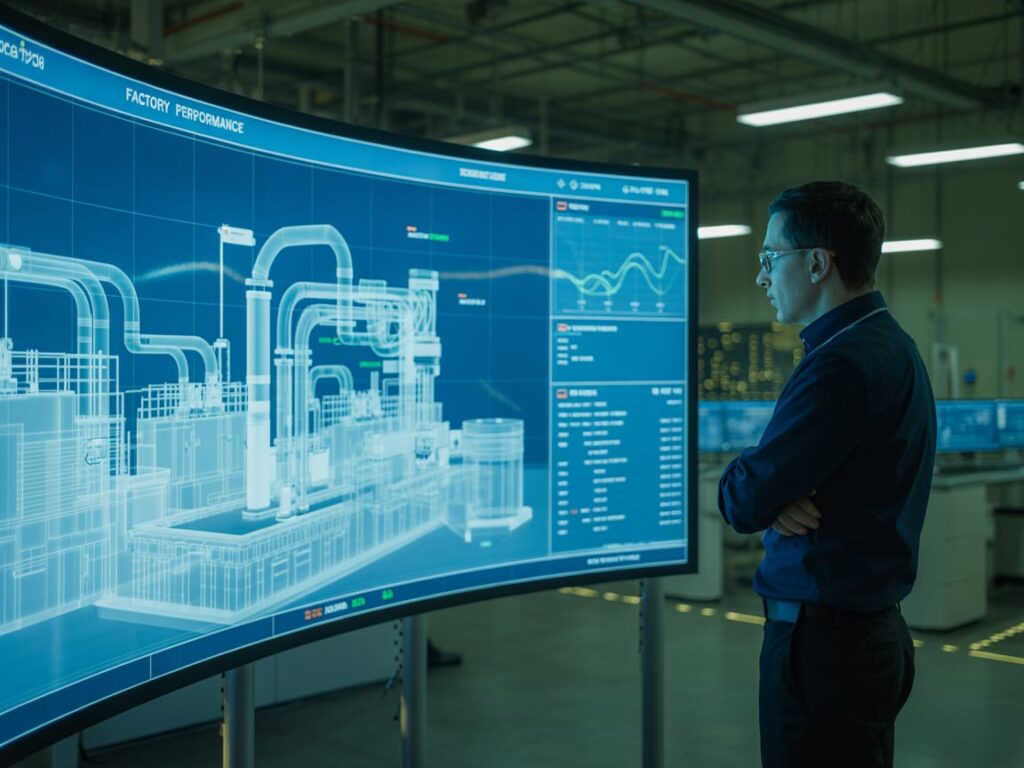
AI and IoT’s Role in Modern RCM
As industries evolve, so does Reliability Centered Maintenance (RCM). The future of RCM is already unfolding, with cutting-edge technologies like Artificial Intelligence (AI) and the Internet of Things (IoT) dramatically improving how we monitor, analyze, and act on asset performance.
1. AI-Powered Predictive Analytics
AI algorithms can process massive datasets from sensors, logs, and environmental inputs to:
- Predict failure patterns
- Identify root causes in real-time
- Recommend optimized maintenance schedules
This reduces human guesswork and allows for dynamic, risk-based planning.
2. IoT-Enabled Monitoring Systems
Sensors embedded in equipment continuously stream data to cloud-based platforms. With IoT, teams gain:
- Real-time visibility into asset condition
- Remote diagnostics
- Automated alerts and predictive maintenance triggers
Combined with RCM logic, these systems automate the decision-making process—helping you stay proactive with less effort.
3. Digital Twins
A digital twin is a virtual model of a physical asset. When paired with Reliability Centered Maintenance (RCM), it allows teams to:
- Simulate failures and consequences
- Optimize task intervals
- Reduce maintenance planning time
4. Mobile and Augmented Reality (AR)
Technicians now use mobile apps and AR headsets to receive step-by-step instructions, log inspections, and scan equipment for instant diagnostics—all tied to RCM task lists.
5. Cloud-Based CMMS + RCM Tools
Cloud solutions ensure global accessibility, automated backups, and integration with business systems (ERP, inventory, compliance tools).
The result? Maintenance becomes more precise, agile, and connected—aligning perfectly with RCM’s goal to maximize reliability while minimizing effort.
Sustainability and Green Maintenance Practices
Modern RCM isn’t just about uptime—it’s also about sustainability. Organizations are under increasing pressure to reduce waste, energy consumption, and environmental impact.
Here’s how RCM contributes to greener operations:
1. Fewer Spare Part Replacements
By only replacing parts when necessary, Reliability Centered Maintenance (RCM) reduces the manufacturing, transport, and disposal waste tied to excess inventory.
2. Lower Energy Use
Efficient equipment performs better and consumes less energy. Reliability Centered Maintenance (RCM) helps ensure that motors, compressors, and pumps operate at peak performance.
3. Extended Asset Life
Longer-lasting equipment reduces the environmental footprint associated with constant replacements and overhauls.
4. Regulatory Compliance
RCM supports compliance with sustainability regulations by documenting proper maintenance, reducing emissions, and improving environmental safety.
5. Data-Driven ESG Reporting
As Environmental, Social, and Governance (ESG) metrics gain importance, companies using RCM can produce cleaner, more transparent records on asset impact.
What’s Next for RCM?
The next generation of RCM will likely include:
- Self-correcting systems that trigger their own maintenance tasks
- Machine learning models that evolve based on new failure data
- More accessible tools for small businesses and facility managers
And as more companies go digital, RCM will shift from a manual process to a fully integrated, automated reliability strategy.
Looking for inspiration? Try UpkeepRecord’s proactive planning ideas that align with sustainable maintenance values.
Frequently Asked Questions About Reliability Centered Maintenance
What is RCM?
RCM stands for Reliability Centered Maintenance, a structured framework used to determine the most effective maintenance strategy for each asset or system. It identifies critical failure modes, assesses their consequences, and outlines preventive or predictive actions to reduce risk and improve reliability.
What is Reliability Centered Maintenance?
Reliability Centered Maintenance is a process that ensures systems continue to perform their intended functions in a defined operating environment. It prioritizes maintenance tasks based on risk and failure impact—combining preventive, predictive, and run-to-failure strategies. It’s not just a task list—it’s a smart, strategic approach to asset care.
What is an RCM in maintenance?
In the maintenance world, RCM is the methodology used to decide what needs to be done to keep equipment reliable. Instead of blindly replacing parts on a fixed schedule, RCM focuses on what can go wrong, why, and what to do about it—often saving time and money.
What does RCM mean?
RCM means applying the right maintenance to the right asset at the right time—not too early, not too late. It’s about balancing safety, performance, and cost-effectiveness by understanding how and why systems fail.
Who has the ultimate requirement to monitor their own reliability?
In practice, the asset owner or operator carries the ultimate responsibility to monitor reliability. Whether it’s a plant engineer, facility manager, or system owner—they must ensure assets meet safety, performance, and compliance standards at all times. RCM provides the framework to do just that.
How is Reliability Centered Maintenance implemented?
RCM is implemented through a structured 7-step process:
Identify functions of an asset
Define how it can fail
Analyze causes and consequences
Rank failures by impact
Choose the best maintenance tasks (preventive, predictive, run-to-failure)
Document and schedule tasks
Review and optimize regularly
Implementation requires a team effort—engineers, technicians, and operations staff working together using data, insights, and technology.
Conclusion: Why Reliability Centered Maintenance Is the Smart Future of Asset Care
In a world where downtime can derail productivity and unplanned failures can cost thousands—or even lives—Reliability Centered Maintenance is no longer optional. It’s essential.
From its origins in the aviation industry to its expanding role in manufacturing, oil and gas, and beyond, RCM has proven to be a precise, effective, and scalable framework. Whether you’re running an industrial operation or managing the upkeep of a small facility, RCM gives you the power to:
- Focus on what really matters
- Reduce unnecessary work
- Increase system reliability and safety
- Save significantly on long-term maintenance costs
Unlike traditional maintenance methods that rely on rigid schedules or wait for things to break, Reliability Centered Maintenance (RCM) invites you to think strategically. It transforms maintenance from a reactive burden into a proactive performance tool—a shift that empowers your team, protects your assets, and boosts your bottom line.
If you’re just starting, begin with one system. Build your team. Ask the 7 RCM questions. Integrate the right tools. Test. Adjust. Grow.
Don’t miss our practical tools and planning advice to complement your RCM journey with everyday maintenance wins.
Let RCM be your new maintenance mindset—not just a method, but a smarter way to take care of everything that matters.